Fuel Oil
aka Heavy oil / marine oil / furnace oil
Fuel oil, also known as heavy oil, marine fuel, or furnace oil, is a byproduct of petroleum distillation. This dense and viscous liquid fuel is commonly used in furnaces, boilers, and engines for heat or power generation, excluding lighter oils with flash points near 42°C (108°F). Fuel oil consists of long hydrocarbon chains, including alkanes, cycloalkanes, and aromatics, and is heavier than gasoline and naphtha.
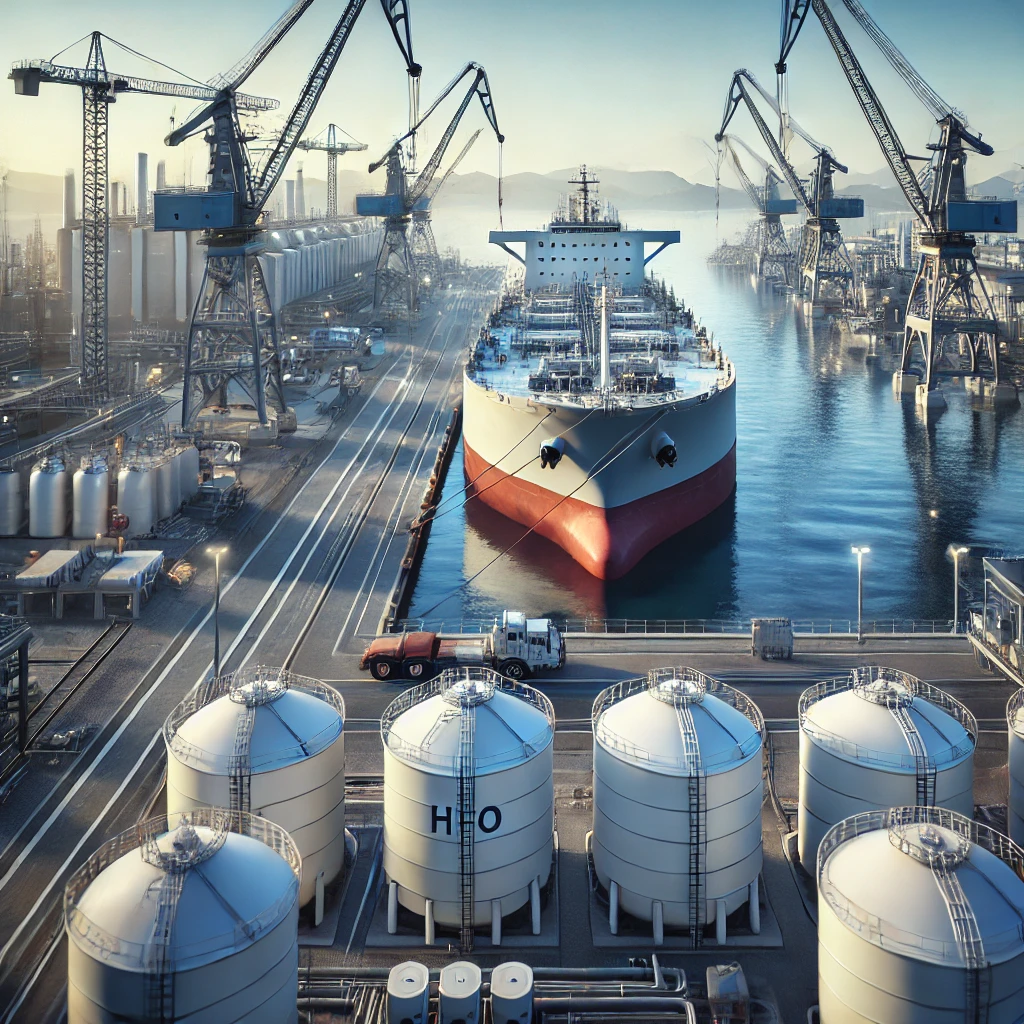
Residual Fuel Oil (e.g., No. 6 Oil):
Residual fuel oil has a high viscosity, requiring preheating to 65–120°C (149–248°F) for storage, pumping, and combustion. This characteristic makes it suitable for use in power plants, large ships, and industrial boilers, which have the necessary space and equipment for proper handling. However, these same requirements make it impractical for smaller vehicles or ships. The high sulfur content and emissions associated with residual fuel oil have further limited its use, as environmental regulations favor cleaner alternatives.
Environmental and Operational Challenges
Environmental and operational issues further complicate the use of residual fuel oil. Its high sulfur content, reaching up to 3% in some cases, contributes to sulfur dioxide emissions, equipment corrosion, and shortened lifespans for heating systems. Cleanup efforts are also challenging, as the oil's viscosity and persistence make it difficult to remediate spills, particularly in aquatic environments. When released into water, residual oil tends to break into tarballs rather than forming a single slick, complicating containment and cleanup efforts.
Modern Applications
Today, fuel oil is still used in specific applications where its cost-effectiveness outweighs its drawbacks. Large ships and power plants continue to rely on it, and it remains an essential component in starting coal-fired boilers, similar to kindling for a fire. However, cities like New York have phased out the most polluting grades of fuel oil as part of broader environmental plans to improve air quality and reduce health risks. While fuel oil remains relevant in certain niches, its role in modern energy production is increasingly limited by environmental and technological advancements.
United States Fuel Oil Grades
Fuel oils in the U.S. are classified by grade numbers, each suited for specific uses: Number 1 Fuel Oil: A volatile distillate, often used in vaporizing pot burners. It is derived from the kerosene cut during distillation and has historical names like coal oil or stove oil. Number 2 Fuel Oil: A common home heating oil, similar to diesel fuel used in vehicles. This grade is sometimes referred to as Bunker A. Number 3 Fuel Oil: Previously a distillate for low-viscosity burners, this grade has been largely absorbed into Number 2 specifications. Number 4 Fuel Oil: A heating oil suitable for burners without preheaters, obtained from the heavy gas oil fraction. Number 5 Fuel Oil: Known as Bunker B, it requires heating to 77–104°C (171–219°F) for proper use. It is often a blend of residual oil and lighter fuel to balance viscosity. Number 6 Fuel Oil: A high-viscosity residual oil, also called Bunker C or residual fuel oil, requires extensive heating and contains impurities like water and mineral soil.
United Kingdom Standards
The British Standard BS 2869 classifies fuel oils for agricultural, domestic, and industrial engines. Heavy fuel oils are commonly used in large-scale applications such as marine engines and industrial facilities.
Marine Heavy Fuel Oil (HFO) for Ships
Heavy fuel oil is widely used in marine engines for propulsion or onboard power generation. Its energy density is measured in megajoules per kilogram (MJ/kg). Under MARPOL Annex 1, HFO is defined by its density and viscosity, often including residual fuels like bitumen and tar. The use of HFO became prominent in the 20th century with the development of internal combustion engines. By the 1960s, motor ships using HFO had largely replaced steamships due to their efficiency and cost-effectiveness. Today, 98% of the global fleet operates on motor ships.
Key Properties of Heavy Fuel Oil
Modern standards such as ISO 8217:2010 specify important properties of heavy fuel oil to ensure safe and efficient use: Catalytic Fines: Residual mechanical particles from refining can damage fuel systems. The maximum allowable content is 60 mg/kg for RMG and RMK categories. Density: This determines ignition quality and is crucial for calculating fuel quantity during bunkering. Viscosity: High viscosity impacts atomization and pumping efficiency, requiring precise temperature control. CCAI: The Calculated Carbon Aromaticity Index measures ignition delay. Higher values indicate inferior combustion quality, with a maximum allowable CCAI of 870 for HFO. Flashpoint: The minimum flashpoint for onboard use is 60°C, as per SOLAS regulations. Pour Point: This is the temperature below which fuel ceases to flow, potentially causing wax formation and equipment blockages. Sulfur Content: Sulfur levels are regulated under MARPOL, with limits of 3.50% m/m (2012) and 0.50% m/m (2020). Water Content: Water contamination reduces efficiency and may cause corrosion. Carbon Residue and Ash: These represent unburned hydrocarbons and inorganic materials, which can cause deposits and efficiency loss.
Environmental and Practical Challenges
While HFO remains cost-effective, its use is limited by environmental regulations and operational challenges. Sulfur emissions and carbon residues necessitate advanced pollution controls. Additionally, improper handling and storage can lead to significant equipment wear and efficiency losses. Fuel oil remains essential for large-scale applications like marine engines and industrial boilers. However, the adoption of cleaner alternatives continues to reshape the fuel oil industry.
Problems with Burning Heavy Fuel Oil (HFO)
Burning heavy fuel oil (HFO) poses numerous challenges onboard ships due to its physical and chemical properties. Water contamination in fuel can reduce efficiency and wear down cylinder liners, often caused by condensation, leaks, or improper storage. Sludge formation is another issue, accumulating at the bottom of bunker tanks and sticking to heating surfaces. If the heating system in bunker tanks fails, the high viscosity of HFO makes pumping it nearly impossible, leading to operational delays and maintenance challenges. Inferior-quality HFO compounds these problems by frequently clogging filters. Mixing different grades of HFO in storage tanks can lead to instability, as limited bunker tank availability on ships forces operators to combine incompatible oils. Combustion issues arise when the oil isn’t sufficiently heated to achieve proper atomization, resulting in carbon deposits on pistons and liners. Additionally, HFO contains abrasive deposits like vanadium, sulfur, and nickel, which can cause wear on liner and piston surfaces. Corrosion is a significant concern, with vanadium reacting with sodium and sulfur to form highly corrosive compounds, while sulfur forms sulfuric acid under certain conditions, causing low-temperature corrosion. Furthermore, lube oil contamination can occur due to leaks or unburned fuel entering the lubrication system, leading to equipment damage and reduced efficiency.
Treatment Methods for HFO Onboard Ships
To address these challenges, HFO undergoes various treatment processes before combustion. Heating is essential to reduce viscosity and improve pumpability. Fuel is heated in bunker tanks, settling tanks, and separators, with temperatures exceeding 80ºC in service tanks to ensure smooth handling and efficient water separation. Draining settling and service tanks further removes water content. Purifiers are critical for separating water and sludge from HFO. Modern purifiers, often computer-driven, enable continuous fuel flow even during sludge discharge. Purification is vital for operational efficiency and is standard on commercial ships. Filtration complements this process by removing solid impurities like fine metal particles that can cause abrasion. Fine filters in the fuel oil supply line ensure cleaner fuel delivery to the system. Chemical treatments, while less commonly used, are employed in some cases to enhance fuel performance. Pre-combustion additives like demulsifiers and dispersants improve fuel stability, while combustion improvers and ash modifiers enhance burning efficiency and reduce residue. By implementing these treatment methods, ships can mitigate many of the operational and environmental challenges associated with burning heavy fuel oil, ensuring smoother operations and reduced maintenance needs.